General
Internal washing of aircraft engines with the ‘Engine Water Wash’ generates considerable cost savings for airlines. Clean engines perform better and consume less fuel.
The engine runs without combustion during washing. Injecting water into the engine at the same time creates a kind of washing machine effect, so the engine cleans itself.
Water and water vapour are released with this method of washing aircraft engines. The water is generally drained off by the general drainage system. The extremely fine water vapour contaminated with heavy metals and kerosene residues remains floating in the air and is harmful when inhaled. Engines are therefore generally washed outside the hangar. Personnel should wear breathing equipment in the vicinity of the process. No other work can be done to the aircraft during washing. Maintenance therefore takes longer. This results in higher costs.
In close cooperation with KLM, U.C. Technologies has developed the EVE for collecting the contaminated water vapour. Engines can be water washed during regular checks in the hangar when the EVE is used.
Contact us thru the button below for more information, or a complete obligation free offer.
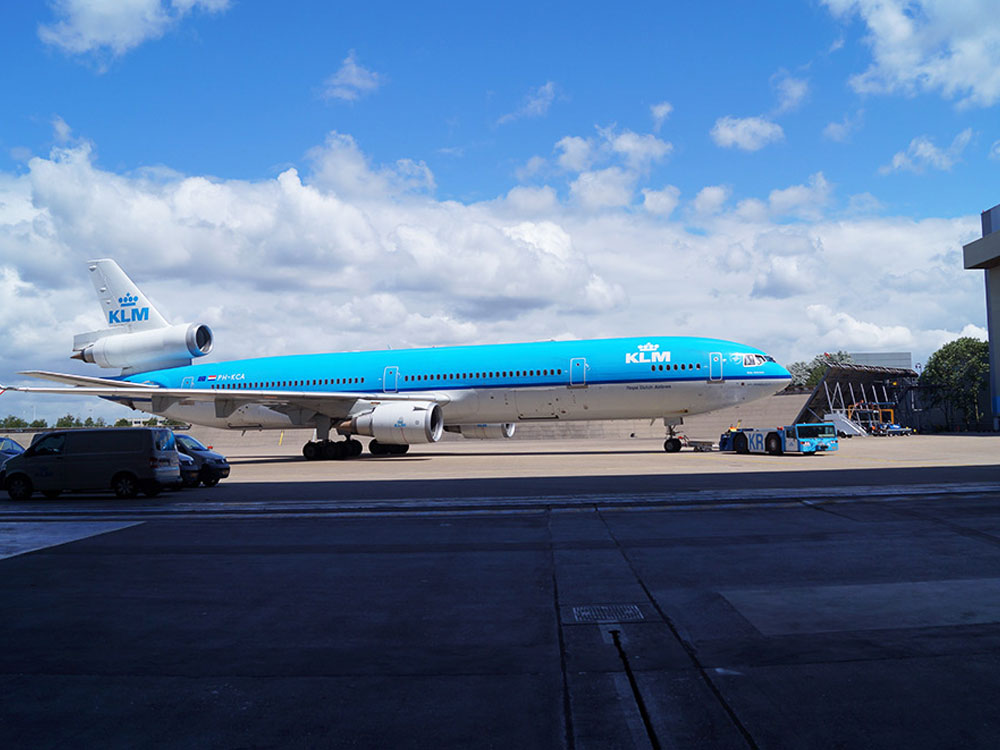
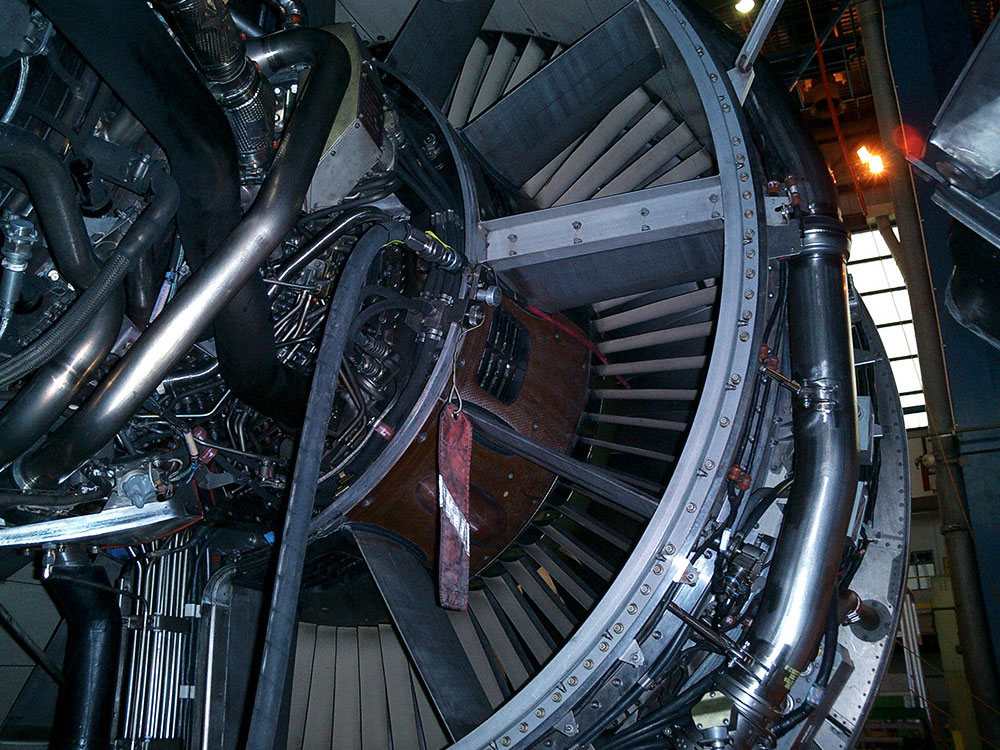
Construction
The EVE consists of the following components:
- Positioning trailer fitted with a 5-axle hydraulically-powered positioning system that positions a plastic cone with an inspection window against the engine exhaust.
- A filter trailer that carries the extraction and filter unit. The hose holder and control box are also installed on this truck.
As there is no mechanical contact between the aircraft and the collector any movement by the maintenance workers in or on the aircraft will not affect the proper functioning or progress of the process. There is no physical contact with expensive engines.
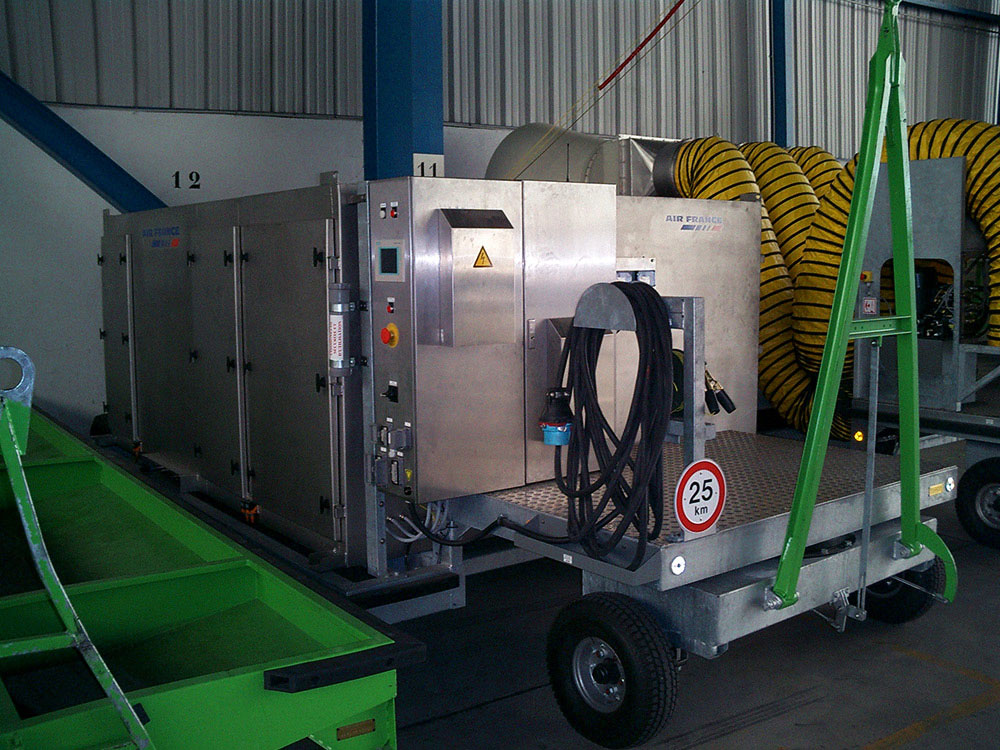
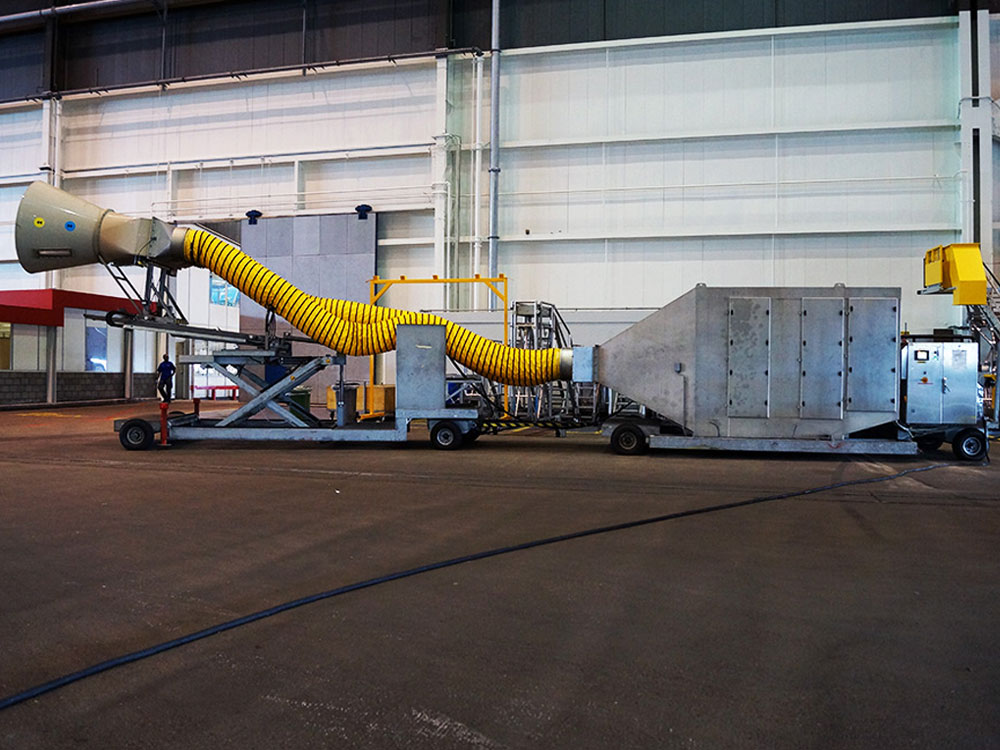
Filtering
- Specially constructed filters remove the heavy metals and kerosene from the collected water vapour.
- The purified air blown out is cleaner than the air in your hangar.
- The filter elements are easily accessible through a hatch in the filter truck and easy to replace.
Water Discharge
The remaining water from the vapour after filtering is collected in the filter housing. A level guage indicates when the filter needs tapping. By connecting a hose, the water is drained away directly, via a drain in your water purification system, for example.
Advantages
- Maintenance personnel need no personal breathing equipment. They can move freely in and around the aircraft without danger to their health.
- The flexible plastic collector cone can be made to fit a wide range of engine types.
- The entire unit has a mobile undercarriage and is easy to tow. Your personnel simply drives the EVE to the workplace.
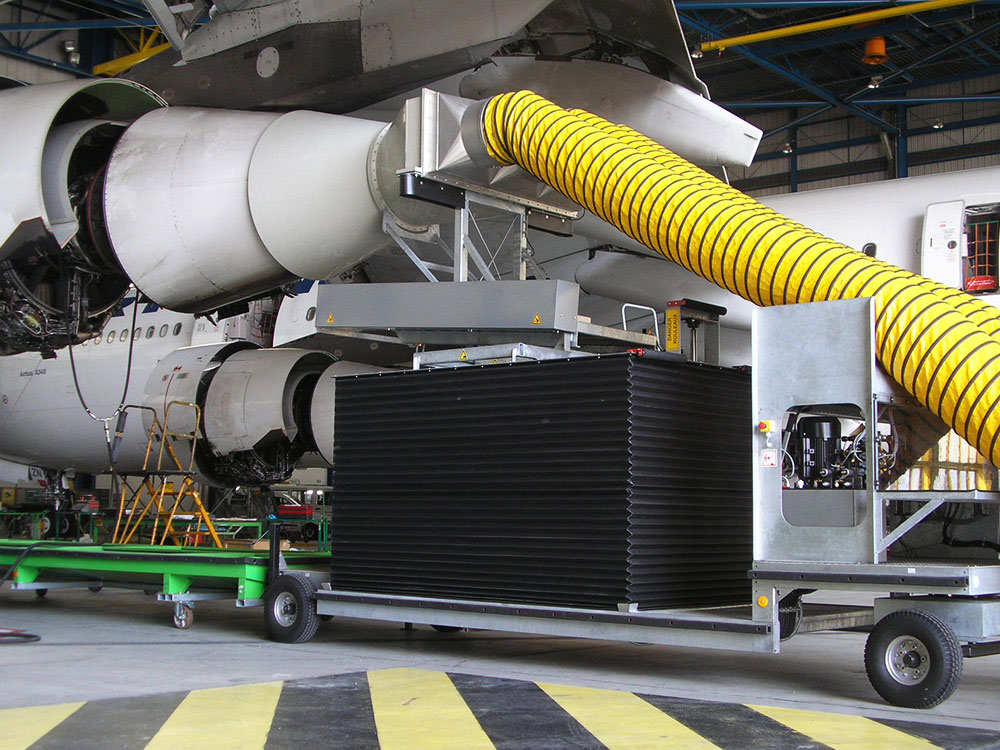
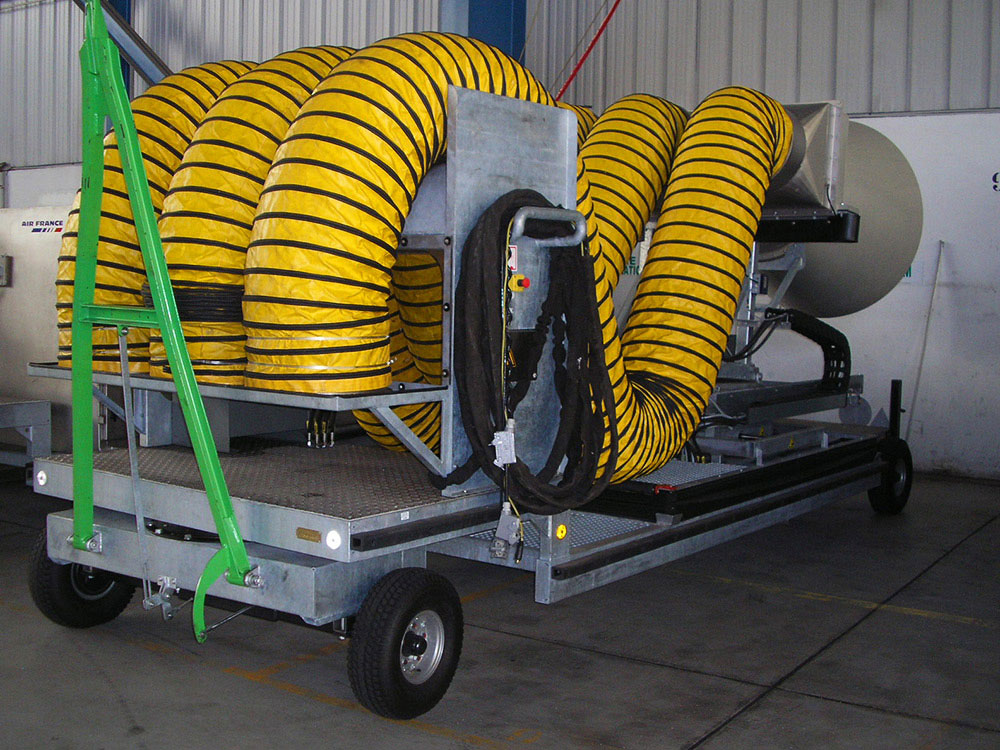